42 Development of the Coal Chemical Industry
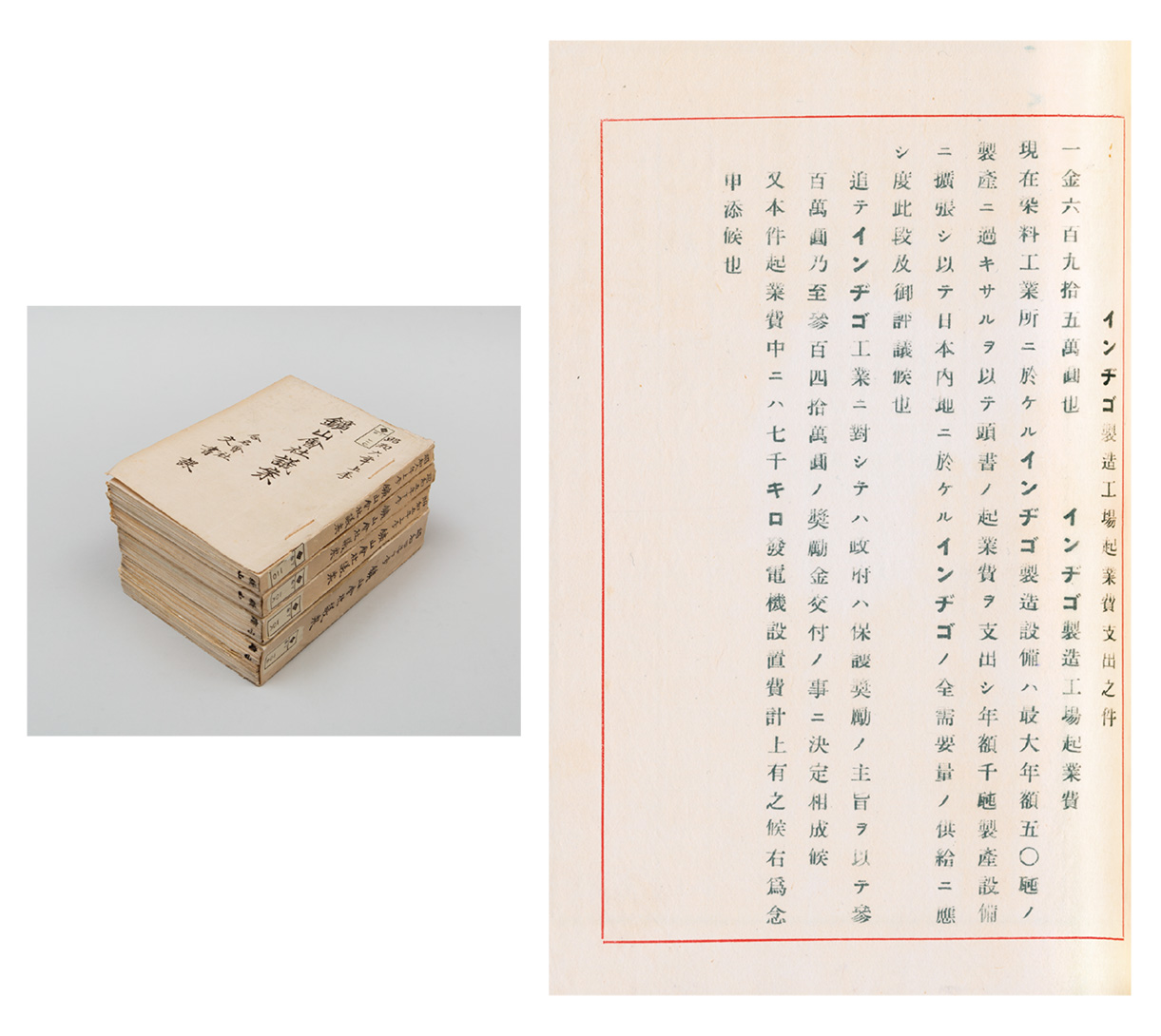
The Dawn of Coal Chemistry
After the Russo-Japanese War, with a domestic economic depression spreading due to the global economic downturn and a worsening of the international balance of payments, Mitsui Mining began a full-scale push into new businesses. Primarily these were chemical industries, mainly zinc refining and synthetic dyes. In Japan at the time, there was a rise in industries like sulfuric acid production, but many chemical products were reliant on imports. For example, zinc, which had anti-corrosion effects, and synthetic dyes, which were rapidly developing internationally, were mostly purchased from Germany.
The catalyst for Mitsui Mining’s coal chemistry business was the expansion of coke production at the Miike Coal Mine for metal refining. By-products generated during the high-temperature dry distillation of Miike coal hindered coke production, leading to the launch of a by-product recovery plan. In 1912, a state-of-the-art Koppers coke oven was built in Omuta (→Fig. 42b) at the suggestion of Nakai Shiro, the head of the coke plant attached to the Miike Coal Mine. At the same time, a succession of by-product recovery plants (a tar distillation plant, a gas plant and an ammonium sulfate plant) also began operation.
The Start of Zinc Refining
At around the same time, Mitsui Mining, which had begun mining zinc ore at the Kamioka Mine in Gifu Prefecture, sent Nishimura Kojiro to Germany for an on-site study of zinc refining. Based on the results of that study, construction was begun on a horizontal distillation furnace in Omuta. In 1923, they successfully produced zinc ingots, and in January of the following year, operations began at the Omuta Zinc Refinery attached to the Kamioka Mine. They took in shipments of coke from the coke plant, and starting in 1915, also began supplying sulfuric acid produced during the zinc ore roasting process.
Domestication of Synthetic Dyes
Once the foundation for the recovery of by-products from coke production was established, Mitsui Mining embarked on research into and development of synthetic dyes. Based on an idea from Makita Tamaki (→Fig. 42c), a plan was advanced to produce alizarin dye using anthracene, a by-product that had previously been of no use. In 1914, an anthracene plant began operating within the coke plant. Two years later, the first domestically produced synthetic dye was released to the market.
Unexpected Success
Mitsui Mining, which had been actively investing in these businesses, generated significant earnings due to the interruption of imports of foreign products cause by the outbreak of World War I. In 1918, as part of a business reorganization, the Omuta Zinc Refinery-which had been operating as one of Japan’s leading zinc refining facilities, attached to the Kamioka Mine-was renamed the Mitsui Mining Miike Zinc Refinery, and became an independent business unit. Similarly, the coke plant, which had been increasing its profits, was promoted to a Mitsui Mining business unit called the Miike Dye Works. Dan Takuma (→33) later expressed surprise at this unexpected success, saying, “It’s remarkable that a business that began as an ‘experiment’ has turned into something like this.” However, once the war ended and imports resumed, the performance of the chemical division worsened sharply. Miike Dye Works in particular suffered significant deficits, which began to generate criticism within Mitsui. Still, with the backing of Dan-Makita’s father-in-law-Mitsui Mining continued to focus its resources on testing and research into new dye businesses.
Industrializing Indigo
Years of effort bore fruit in 1926, when Mitsui Mining succeeded in the industrialization of the production of indigo, which had seen a sharp rise in imports at the time. As noted in the historical record seen at the top, in 1929 a plan for mass production of indigo was decided on with the support of a subsidy from the government, and three years later, a plant for producing synthetic indigo went into operation. The indigo produced there met most of the domestic demand, nearly achieving the government’s goal of holding off imports. Beyond that, the company also expanded its sales channels for “Mitsui Indigo” overseas.
A Coal Chemical Industrial Complex
Riding the momentum of its success with indigo, Mitsui Mining began a full-scale expansion into the ammonia synthesis and ammonium sulfate business. In 1931, Miike Nitrogen Industry was established, followed by Toyo High-Pressure Industry two years later, both in Omuta. Miike Dye Works and the Miike Zinc Refinery, both business unites of Mitsui Mining, along with affiliated companies such as Denki Kagaku Kogyo, Miike Nitrogen and Toyo High-Pressure grew while maintaining technical relationships with one another. The effective utilization of by-products thus led to the formation of a coal chemical industrial complex in Omuta, where a cross-exchange of raw materials and semi-finished products could be accommodated within a specific region.
Important deals decided by the Board of Directors of Mitsui Mining had to first be submitted to and approved by Mitsui Gomei Kaisha (→39). This item refers to the expansion of equipment at the indigo manufacturing plant at Miike Dye Works (later Mitsui Chemical Industries), a business unit of Mitsui Mining, which was approved on October 26, 1929. The industrialization of indigo production was a symbolic event that elevated the reputation of Miike Dye Works and marked a turning point in accelerating Mitsui’s expansion in the chemical business sector.
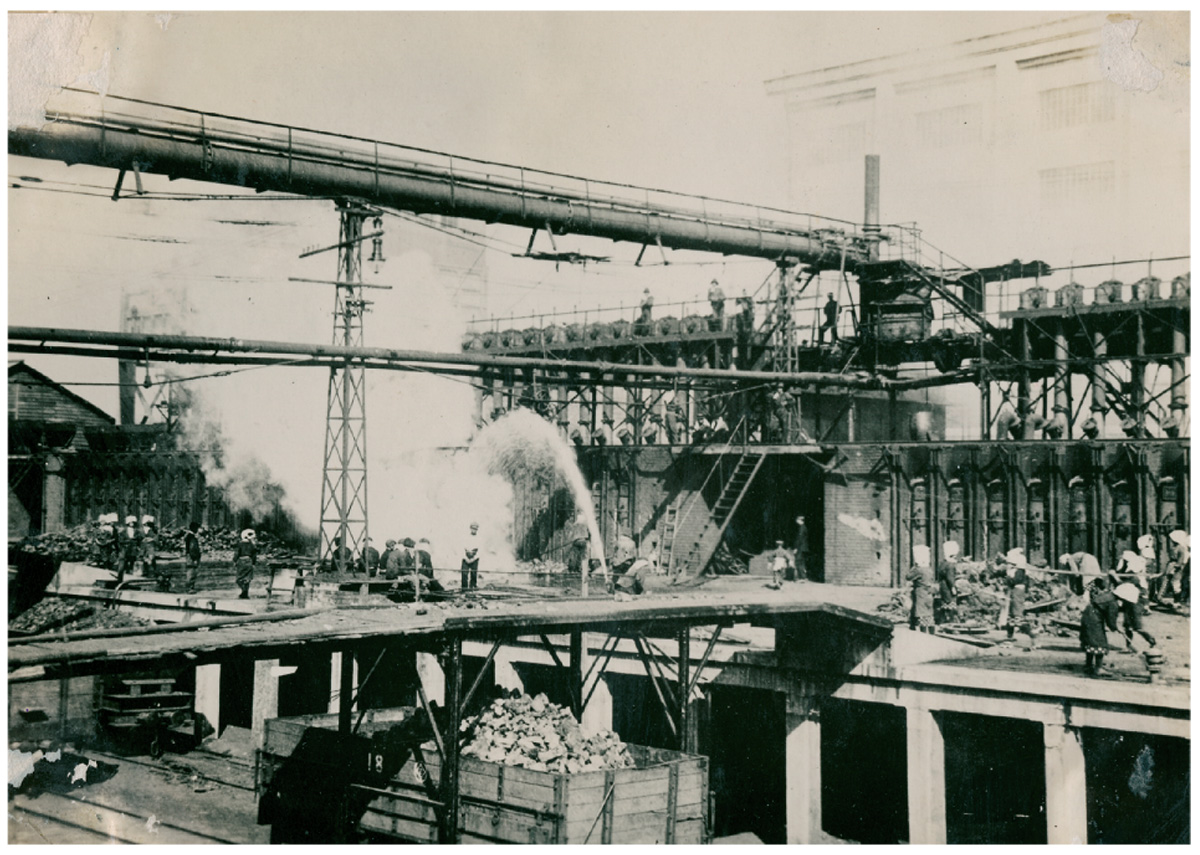
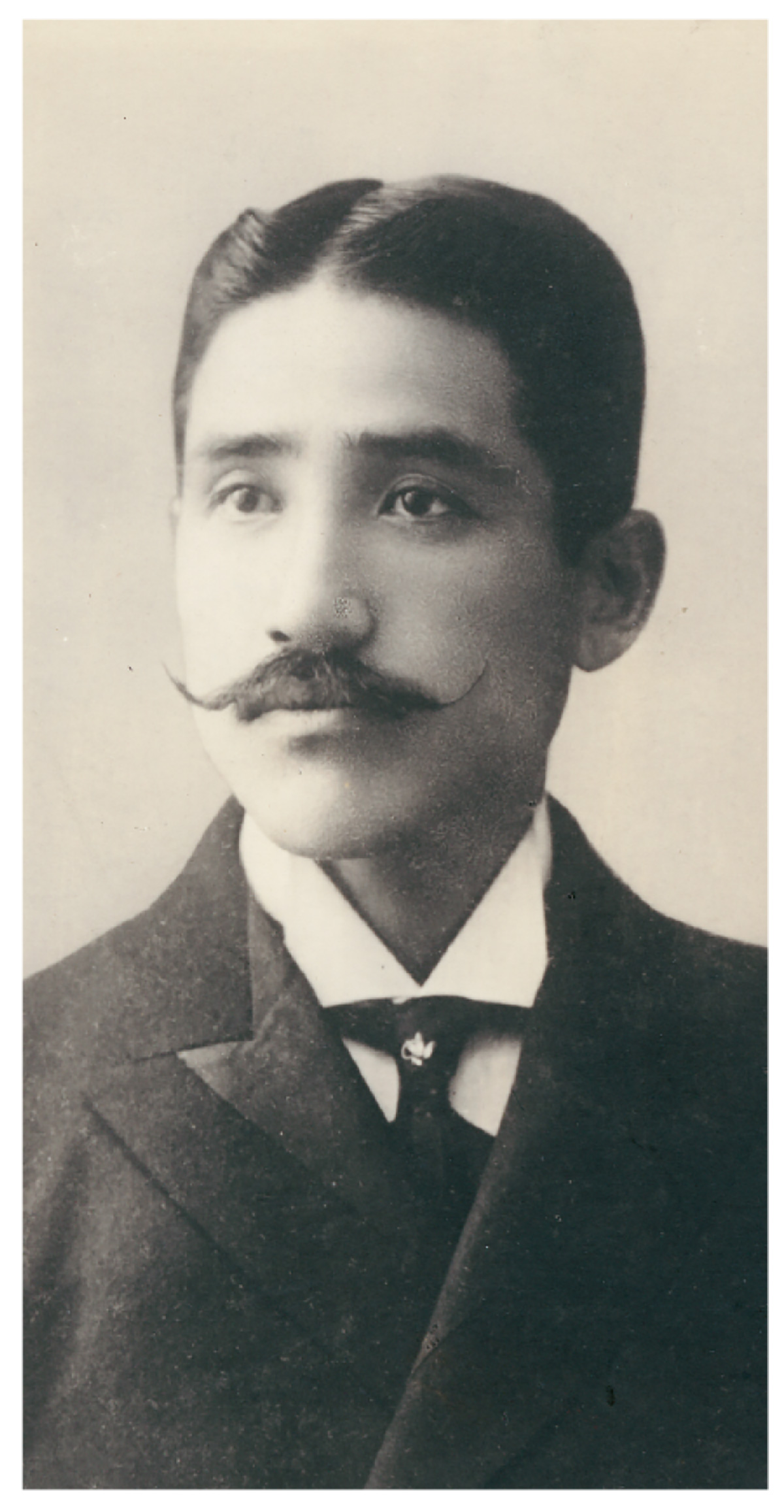
After joining Mitsui Mining in 1895, he contributed significantly to projects such as the construction of Miike Port. In 1902, he married Dan Takuma’s eldest daughter, Meiko. He became a director at Mitsui Mining in 1913, and after Dan’s assassination in 1932, went on to become an executive of Mitsui Gomei Kaisha.